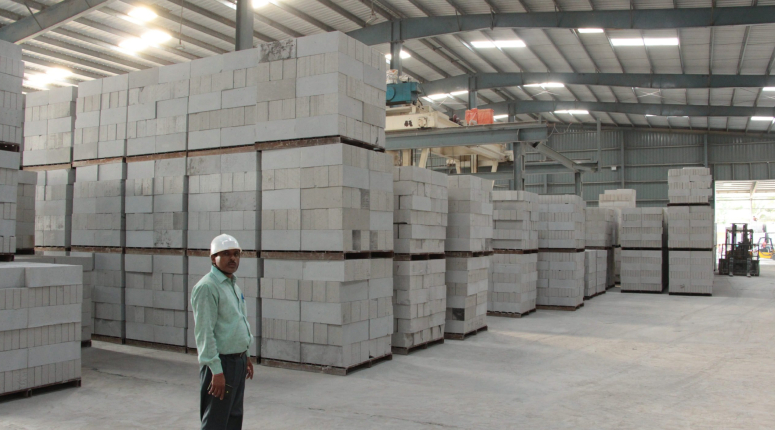
Superlite AAC Blocks
Autoclaved Aerated Concrete (AAC), also known as Autoclaved Cellular Concrete (ACC),Autoclaved Lightweight Concrete (ALC) is a lightweight, precast, foam concrete building material invented in the mid-1920s that simultaneously provides structure, insulation, and fire – and mold- resistance and various other advantages. It is also an environment friendly product, as it is manufactured using 65-70% of sand/ fly ash (by weight). Due to its many desirable attributes, AAC Blocks have gained massive popularity in Northern, Western and Southern India with almost 80 percent of the constructions using AAC Blocks as a replacement of the traditional fried clay bricks. In the North Eastern region, it is gaining popularity since 2012 and is looking to completely replace the use of traditional fired clay bricks. AAC was perfected in the mid-1920s by the Swedish architect and inventor Dr.Johan Axel Eriksson, working with Professor Henrik Kreuger at the Royal Institute of Technology. The process was patented in 1924. In 1929, production started in Sweden at the city of Yxhult. From “Yxhult Anghardade Gasbetong” later became the first registered building materials brand in the world: Ytong. The second major international cellular concrete Hebel brand goes back to company founder and technicians Josef Hebel from Memmingen. In 1943, the first Hebel-plant was opened in Germany.
Originally Ytong autoclaved aerated concrete in Sweden was produced with alum shale, whose combustible carbon content made it beneficial to use in the production process. Unfortunately, the slate deposits used for Ytong in Sweden also contains a very low level of natural content uranium, which makes the material give off radioactive radon gas to the building. By using new recipes, containing only Quartz sand/ Fly ash, Calcined gypsum, Lime(mineral),Cement, Water and Aluminum powder, after 1975, Ytong produced a new type of aerated concrete blocks which doesn’t contain alum slate anymore and thus the problem of radon exposure from this raw material eliminated since this time. The production of this white autoclaved aerated concrete is state of the art since those days and similar recipes are used by all producers all over the world.
Superlite Brochure &
Superlite AAC Blocks Installation Guidelines
COMPOSITION OF AAC BLOCKS
COMPOSITION OF AAC BLOCKS
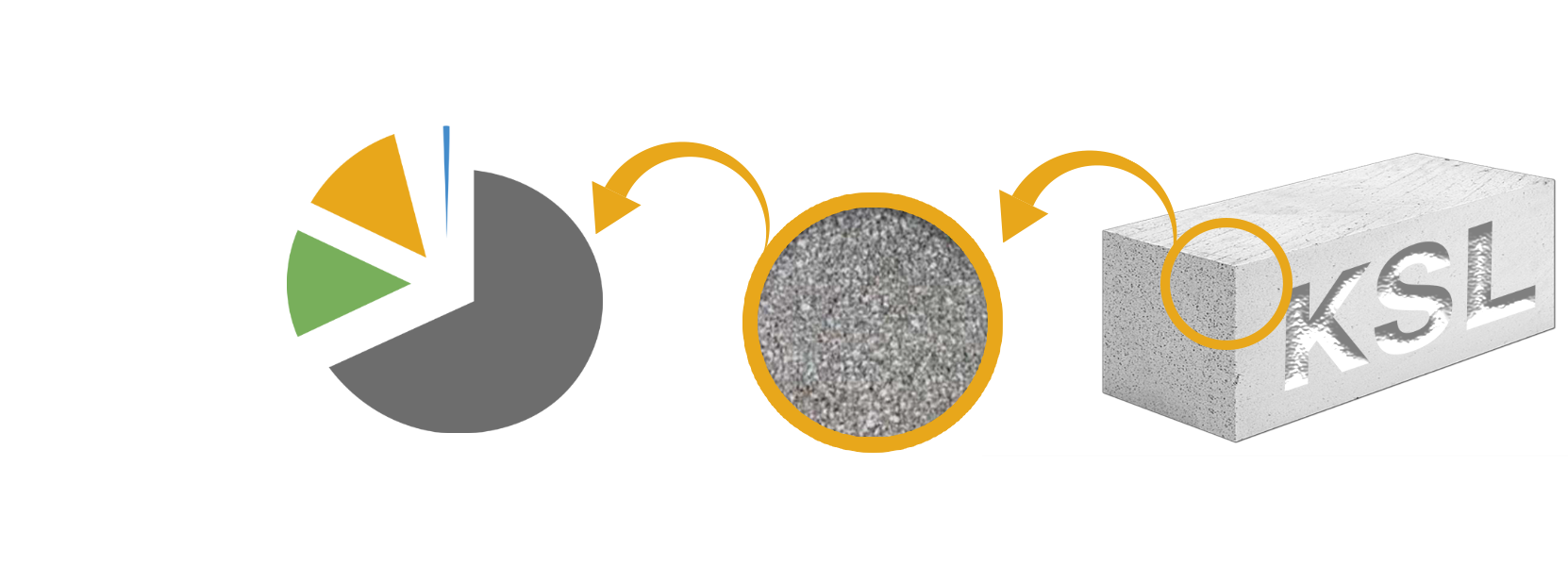
MANUFACTURING PROCESS
MANUFACTURING PROCESS
The Aerated Autoclave concrete consists of mainly two process- Aeration and Autoclaving.
- 1. The aeration process is due to reaction between quick lime and aluminum powder. In aeration process lime reacts with aluminum powder to produce Tricalcium Hydrate and Hydrogen. This leads to rising of the cake and makes the blocks truly lighter.
- 2. Autoclaving is the process of producing high pressure and high temperature steam curing in close vessels. Autoclave is a long vessel with a temperature of about 185 degree and pressure at about 700 Kpa. AAC blocks undergo autoclaving for about 14 to 18 hours. This provides required strength to the blocks.
DETAILS
DETAILS
Unlike most other concrete applications, AAC is produced using no aggregate larger than sand. Quartz sand, calcined gypsum, lime (mineral) and/or cement and water are used as binding agent. Aluminum powder is used at a rate of 0.05%–0.08% by volume (depending on the pre-specified density). In some countries, like India and China, fly ash generated from thermal power plants and having 50-65% silica content is used as an aggregate.
When AAC is mixed and cast in forms, several chemical reactions take place that give AAC its light weight (20% of the weight of concrete) and thermal properties. Aluminum powder reacts with calcium hydroxide and water to form hydrogen. The hydrogen gas foams and doubles the volume of the raw mix creating gas bubbles. At the end of the foaming process, the hydrogen escapes into the atmosphere and is replaced by air.
When the foams are removed from the material, it is solid but still soft. It is then cut into either blocks or panels, and placed in an autoclave chamber for 12 hours. During this steam pressure hardening process, when the temperature reaches 190° Celsius (374° Fahrenheit) and the pressure reaches 8 to 12 bars, quartz sand reacts with calcium hydroxide to form calcium silica hydrate, which gives AAC its high strength and other unique properties. Because of the relatively low temperature used AAC blocks are not considered fired brick but a lightweight concrete masonry unit. After the autoclaving process, the material is ready for immediate use on the construction site. Depending on its density, up to 80% of the volume of an AAC block is air. AAC’s low density also accounts for its low structural compression strength.
Since 1980, there has been a worldwide increase in the use of AAC materials. New production plants are being built in Australia, Bahrain, China, Eastern Europe, India, Israel, and the USA. AAC is increasingly used by developers, architects, and home builders worldwide
QUALITY CONTROL
QUALITY CONTROL
At SUPERLITE, Quality is of paramount importance, as we intend to provide our customers/end-users, finest product of highest standard of quality & strength. For this end in view, rigorous Lab tests of all input material – whether it is Cement, Lime, aluminum powder or gypsum or other essential additives- are conducted prior to application in production process. Then, at every stage of production, random tests are undertaken at regular interval during the batch process. Thereafter, the final product is subjected to required physical & chemical Tests including the Compressive Strength Test of random samples drawn from each batch, to ensure that each Block is of Grade-I as per laid down parameters of IS:2185 (Part-3):1984. In fact, the beauty of SUPERLITE AAC BLOCKS lies in its high compressive strength while maintaining the light weight of the blocks.
BENEFITS & FEATURES
TECHNICAL ADVANTAGES
Earthquake Sustainability
Due to its light weight & porous structure consisting of millions of tiny cells (air pockets), AAC Blocks provide cushion to buildings from major force or jolts, preventing progressive collapse, saving lives and granting better response time for rescue operation
Thermal Insulation
AAC Blocks offer excellent thermal insulation of rating of R30. This reduces recurring cost of energy required for heating and cooling. Better thermal insulation also allows use of smaller HVAC than required conventionally.
High Strength
High pressure steam-curing & autoclaving process gives Superlite AAC Blocks exceptional strength to weight ratio, much above BIS specification of > 3.5Mpa.
Fire Resistance
Best in class fire rating of 4 hours. The melting point of AAC is over 1600 c, more than twice the typical temperature in a building fire of 650C.
Sound Resistance
AAC walls have an excellent Sound Transmission Class (STC) rating of 44 dB. Result: Virtually Soundproof Interiors!
Cost Saving
Saving in Steel & concrete reinforcement up to 20%, Saving in Mortar Usage and Saving in Plaster Usage.
No Curing
AAC blocks’ walls do not require water curing (i.e. soaking the entire plastered wall with water spray), as needed by red-brick walls. AAC blocks are already pre-cured.
Conservation of fertile land
In case of red bricks, fertile top soil is used exploiting the utility of fertile land. However in case of AAC Blocks, we use Fly Ash i.e. an industrial waste and river sand.
Precise Dimensions
Its automatic manufacturing process gives AAC an exceptional dimensional accuracy & smooth surfaces, eliminating need of three-coat plaster walls and allows for a final 6 mm skin coat (Putty/POP).
Pest Resistance
Pest Resistant with solid wall construction and finishes, there are fewer if any, cavities for insects and rodents to dwell in. Termites and ants do not eat or nest in AAC blocks. Being made up of inorganic mineral, AAC blocks do not promote growth of molds.
Environmental Impact
Every input and process of Superlite AAC Blocks’ manufacture is 100% environment friendly. We are proud members of Indian Green Building Council.
Workability
AAC Blocks can be sawed, drilled, just like wood, and thus is a very good construction material to be used. It facilitates easier fitting of plumbing, electrical and also wall fittings.
COST SAVING
COST SAVING
- Saving in Mortar Usage: Due to the massive size of AAC Blocks as compared to red bricks, the no. of joints is reduced by 65% and hence the usage of mortar is reduced by 60%.
- Saving in Mortar Usage: Due to the massive size of AAC Blocks as compared to red bricks, the no. of joints is reduced by 65% and hence the usage of mortar is reduced by 60%.
- Faster Construction: AAC Blocks due to its 7 times bigger size than red bricks ,the ease of laying with 1/3 no. of joints ,precise dimensions and no curing requirement ,offers time saving up to 30%.And so you see your project completed within a much shorter time frame as compared to red bricks.
- Saving in financing cost: Money borrowed/invested in a project has its financing cost or opportunity cost. The sooner the project completes the sooner it becomes ready to yield utility and it saves your financial cost i.e. interest charges.
- Saving in Man-hours (Labor): Man-hours is a substantial cost for construction. AAC Blocks due to its 7 times bigger size than red bricks, the ease of laying with 1/3 no. of joints ,precise dimensions and no curing requirement, offers time saving i.e.labor charges of up to 40%.
- Saving in Transportation: Transportation/Freight is a major cost head for AAC Blocks to reach the site of the customer. For this, the weight of the blocks play an important factor to decide the freight since by road the cost of transportation is based on weight of the product.AAC Blocks being 1/3rd in weight as compared to red bricks,it is much cheaper to transport AAC Blocks rather than red bricks.
- Saving in cost of undercoat and top coats. The requirement of undercoats is highly dependent on the kind of smoothness of the wall installed. The wall that is made of AAC Blocks offers you highly smoother wall as compared to that of red bricks and hence the wall does not require undercoat such as putty/pop .
Cost Impact Analysis
Cost Impact Analysis
Cost Component | Saving in Component | Estimated Impact On Project Cost | Explanation |
---|---|---|---|
Mortar Material | 60% | 2% | Superlite AAC Blocks are 7 times the size of conventional bricks, resulting in 1/3rd the number of joints. Thus an overall mortar savings up to 60% |
Plastering Material | 35% | 2% | Exceptional dimensional accuracy & smooth surfaces, eliminates need of three-coat plaster walls & allows for a final 6 mm skin coat (putty/gypsum plaster). |
Wastage | 10% | 0.50% | Breakage in Bricks might be as high as 15% which in case of AAC blocks is less than 5%. |
Structural Material (Steel & Concrete) | 20% | 8% | Being light weight, AAC blocks drastically reduce the dead weight of the building. This translates to design of lighter structures leading to reduction in steel and concrete (up to 20%) |
Savings in Capex for HVAC Systems | 30% | 0.50% | AAC blocks have excellent insulation properties, which results in saving in capex & opex of HVAC systems. |
Total Impact on Project Cost | 13.00% |
Technical Specifications
Technical Specifications
Parameter | Value |
---|---|
Normal Dry Density | 551 - 650 kg/m3 |
Compressive Strength | 4 N/mm2 (MPa) |
Thermal Conductivity | 0.24 w/m0K |
Drying Shrinkage | 0.04% |
Fire Rating | 4 Hrs |
Sound Transmission Class Rating | upto 42 dB |
Dimensions and Weight
Dimensions and Weight
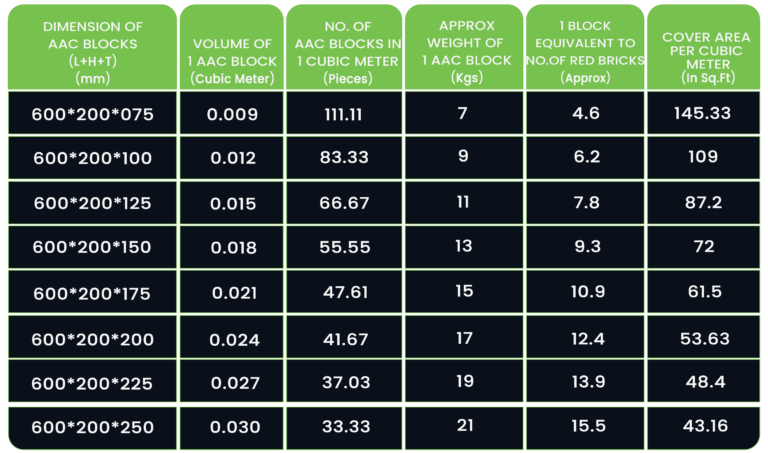
- The above data is correct to an approximate value.
- The above coverage area is considering 3mm thickness of joining mortar.
Comparision between AAC Blocks & Red Clay Bricks
The Diffrence
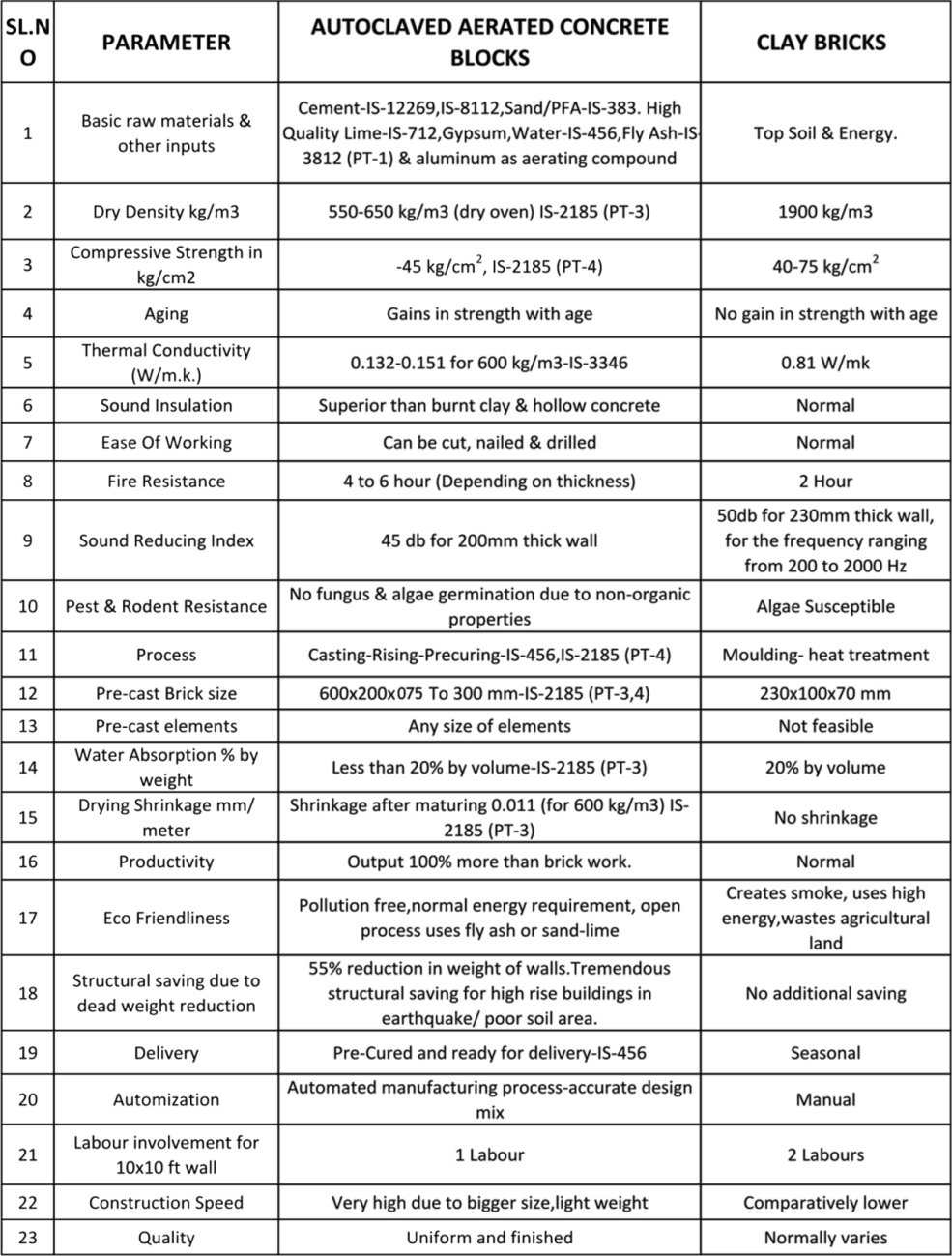
Approvals, Our Clients & Certification
Approvals, Our Clients & Certification
Approvals | Our Clients | Certifications |
---|---|---|
CPWD | SHREE GAUTAM CONSTRUCTION COMPANY LTD | BUREAU OF INDIAN STANDARDS |
PWD-ASSAM,MEGHALAYA | NCC LIMITED | INDIAN GREEN BUILDING COUNCIL |
IIT | TRIBENI CONSTRUCTION LTD | BHUTAN STANDARD BUREAU |
NIT | BRAHMPUTRA INFRASTRUCTURE LTD | |
MES | BHARTIA INFRA PROJECTS LTD | |
RITES | KMV PROJECTS LTD | |
POWERGRID | DHAR CONSTRUCTION | |
NBCC INDIA LTD PROJECTS | BADRI RAI & COMPANY | |
NHM | M.P. KHAITAN | |
EPIL | ROYAL GROUP | |
POWERGRID CORPORATION LTD | SRINATH BUILDERS AND HOUSING CO. PVT. LTD | |
SM JDB ESTATES PVT. LTD | ||
ARUNODAYA CONSTRUCTION COMPANY |